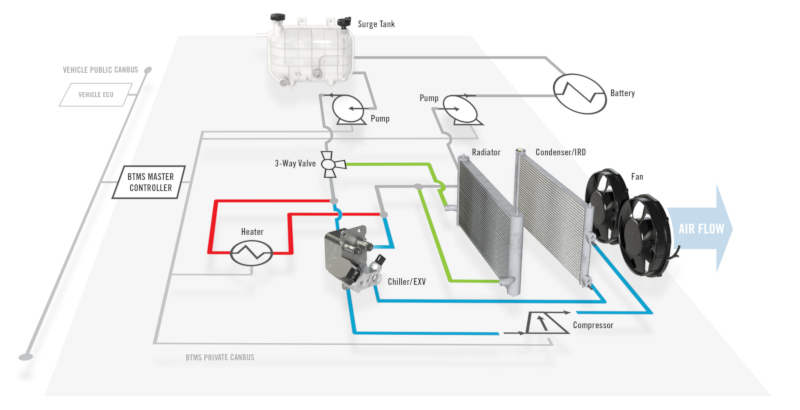
How It Works: Battery Thermal Management System
The Li-Ion battery cells used in today’s commercial electric vehicles are sensitive to temperature which will impact performance of the battery pack including range, voltage efficiency, charge time, and also improve cycle life of the battery pack.
- Cold battery pack temperatures can reduce the charge/ discharge capacity and power capabilities of the battery pack, as the chemical reaction inside the battery slows down, raising the internal resistance.. In extreme cold (typically below 0°C), the battery may even stop functioning. In most cases, below -20°C, the battery pack can even see irreversible damage.
- Higher battery pack temperatures can also result in performance degradation including loss of capacity and power. Loss of lithium and the reduction of active materials under high temperature is what results in loss of capacity, and increase in internal resistance is what contributes to loss of power. Similar to extreme cold, extreme high temperatures (typically above 60°C) can also result in the battery pack not functioning and in some cases, results in irreversible damage. In the worst case, a thermal runaway can even trigger self-ignition and explosion.
A Battery Thermal Management System, or BTMS, helps to maintain a battery pack at its optimal temperature range of 20o to 45oC regardless of ambient temperature. For each vehicle design, the required performance and cycle life of the battery pack will be considered to determine the specific set point for the battery pack temperature.
A full-featured BTMS schematic is shown to the left. In liquid-cooled battery packs, coolant will flow through the battery’s BMS (Battery Management system) to transfer heat to and from the battery cells to the coolant either through direct immersion or conduction through a battery plate or other structure. This coolant from the battery pack outlet port will then flow through the Battery Thermal Management System for conditioning. The BTMS has two primary functions Heating or Cooling:
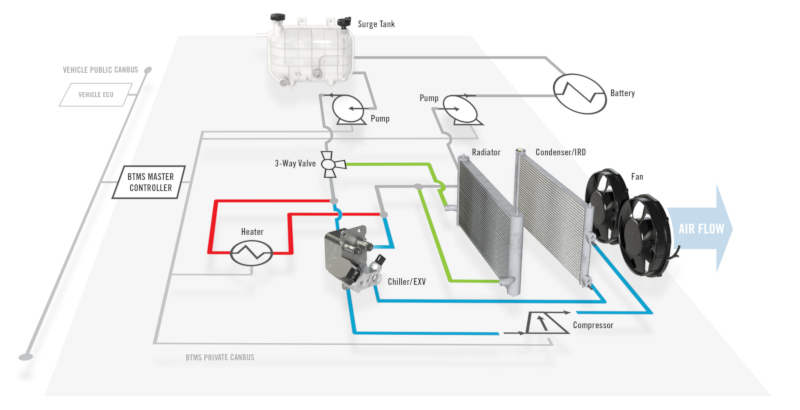
- Heating: In cold ambient conditions, the battery pack may need to be heated to facilitate charging/ pre-conditioning and getting the pack temperature to ideal range. The BTMS heating loop includes a high voltage (HV) electric heater to warm the coolant to the desired set point .
- Passive Cooling: The battery pack will generate heat during charging and when the vehicle is in operation/ discharging. This heat needs to be managed to allow the battery pack to be at the desired set point. If the ambient temperature is far enough below the battery pack temperature, a passive cooling loop can be used to reject heat from the coolant loop. This loop has a radiator to reject heat from the coolant to ambient air, and an array of fans to increase air flow through the radiator to maximize heat transfer. The fan array will use less power than the refrigerant loop in the Active Cooling circuit improving co-efficient of performance of the BTMS, thus improving range of the vehicle.
- Active Cooling: When ambient temperature is above the battery pack temperature, an active cooling loop with a refrigeration circuit will be required. In this loop, heat is transferred from the coolant to a refrigerant through a chiller. Since a refrigeration circuit requires a compressor for cooling, the Active Cooling loop draws more power when in operation than passive cooling.
A BTMS is designed to be a complete, plug-and-play system including all necessary heat exchangers, smart electric products, wiring and hoses, as well as a thermal master controller and a tailored firmware to provide complete operation upon delivery, enabling fast and easy integration into the vehicle’s chassis.
An integrated master controller in the BTMS communicates with the vehicle control unit (VCU) to get input signals like average battery pack temperature (set-point) and the mode of BTMS operation. When in auto mode, the BTMS controller uses the set-point to intelligently control operation of the different circuits within the BTMS in the most efficient manner A BTMS will also include multiple pressure and temperature sensors to allow the master controller to monitor and optimize operation. The BTMS master controller sends a wide range of critical information and fault codes to the VCU to facilitate vehicle level monitoring, diagnostics and troubleshooting.